A leading chip manufacturer aimed to build an advanced Pick & Place machine with a placement capability of > 72,000 CPH (Components per Hour). To this end, they designed a machine with 32 head units and a double gantry system with component-pressing force control. The machine placement mounting head units needed to move extremely fast and in coordinated motion trajectories, and be capable of immediately switching to very low and accurate controlled force. For the motion control solution, they turned to Elmo.
Read this case study to learn about:
- How a customized Elmo solution enables the machines to operate in extreme environment under extremely high acceleration G’s.
- Smart servo drives providing high precision and accurate sensor-less force control.
- How the machines double their throughput using highly synchronized double gantry system, powered by Elmo.
- > 40% shrinking in machine size and weight with increased servo performances.
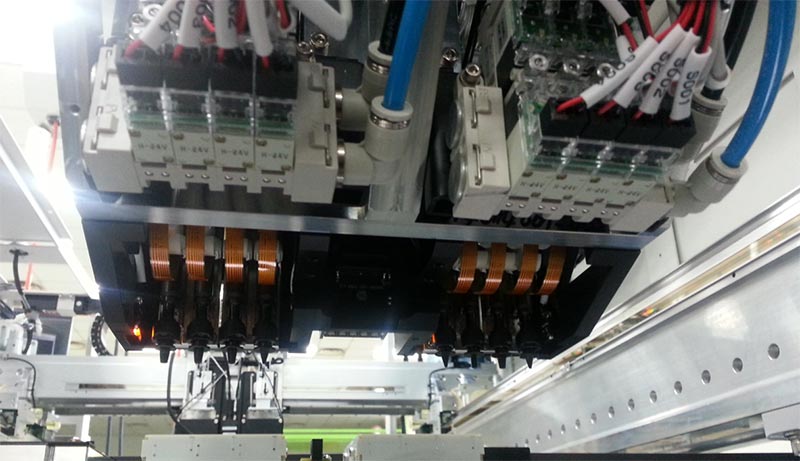
The Machine’s Requirements
A new generation of Pick and Place machinery has demanded that in addition to producing fast throughput and very high accuracy, it would control with high precision the mounting force of the placed components.
One of the many challenges implemented in this machine was to realize very low and precise component pressing forces in the range of 0.3N to 20N followed by extremely fast coordinated point to point motions. Meeting the very high throughput challenges is best solved by very “agile and light” mechanics. This introduced parasitic resonances and crucial non-linearity. The unwanted oscillation had to be removed, either by costly improvements of the existing mechanics or by smart servo drives’ assembly that is rugged enough to withstand those extreme mechanical vibrations and shock.
The Elmo Motion Control Solution
- Gold Twitter servo drives
The solution to the machine’s unique requirements was a customized, integrated board with four standard Gold Twitter drives from Elmo. Each machine has a double MIMO (multi-input-output control) rigid gantry system that controls 32 Gold Twitter servo drives (eight boards) through one, coordinated motion EtherCAT network. The Gold Twitter drives are located in a dense and harsh moving environment (on the Gantry rigid bridge) and move at high Gantry speeds of up to 2m/sec. Elmo’s drives perform all the critical tasks of fast and accurate X&Y&Θ control in conjunction with a very fast and precise force control of the Z-axis of the mounting head. In order to set a very precise controlled force on the final tip tool, a linearization function in the Gold Twitter was applied.
The drives are operating in a very dense, harsh and extreme undefined mechanical vibrations environment while keeping the highest machine performances, as fast motion speeds and precise, accurate low force control set a new challenge in this kind of application machine motion control solutions.
The Outcome
Elmo provided a motion control solution that could withstand the harsh environment under extremely high acceleration G’s while reducing the machine footprint (size and weight) by 40%. With the Elmo drives, the machine has doubled its throughput while maintaining uncompromised quality.
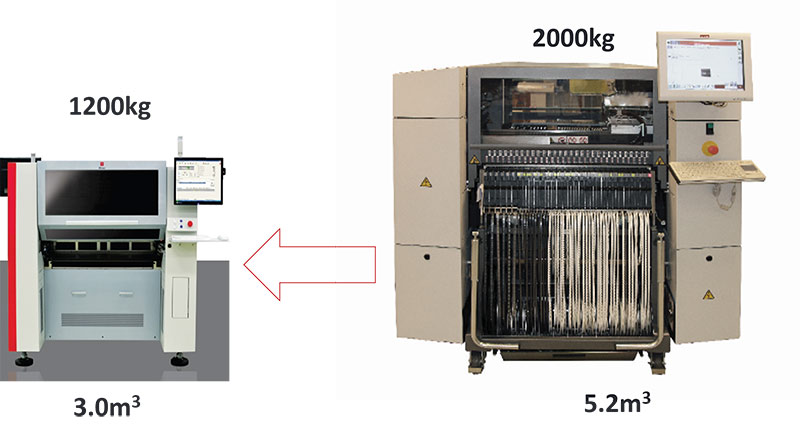
> 40% shrinking in Machine Size and Weight
For More Information