Description
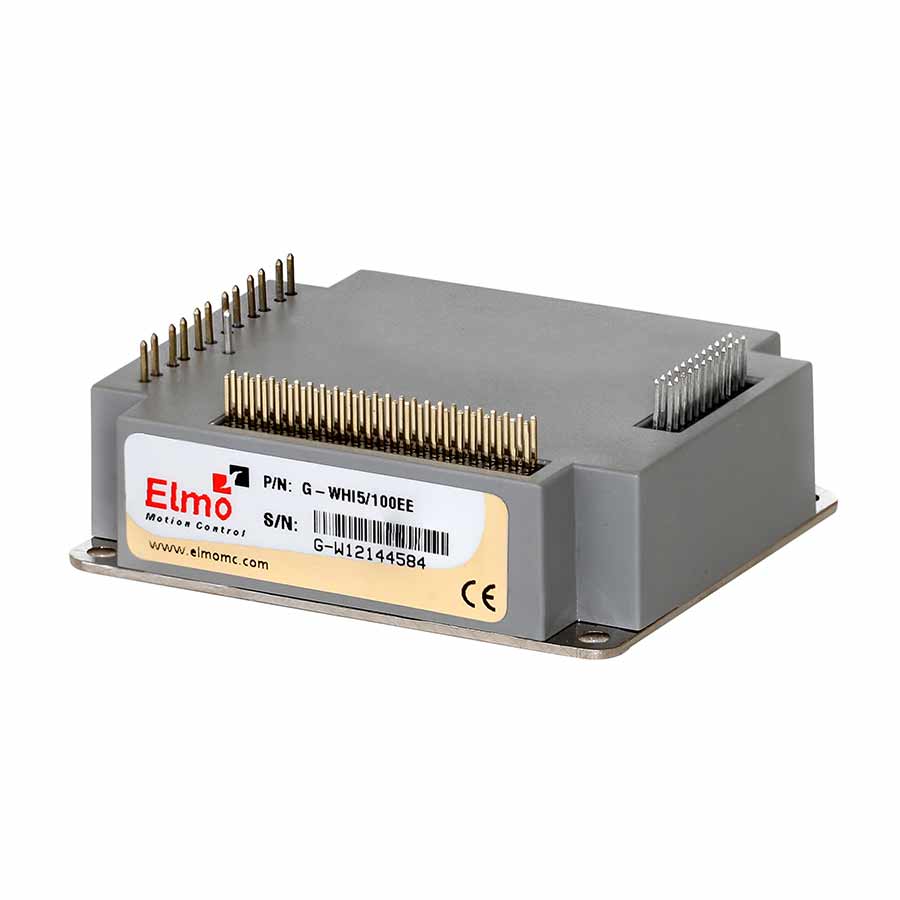
Miniature, Network-based Servo Drive
Up to 20 A/100 V and up to 9 A/200 V
Up to 1.6 kW of continuous power
The Gold Whistle is a compact, PCB-mounted digital servo drive that weighs just 55 g (1.94 oz) and offers up to 1.6 kW of continuous power or 3.2 kW of peak power.
This advanced, high power density servo drive provides top performance, advanced networking and built in safety, as well as a fully featured motion controller and local intelligence. The Gold Whistle is powered by a single 12 V – 95 V isolated DC power source (not included) and a “smart” control-supply algorithm enables the drive to operate with only one power supply with no need for an auxiliary power supply for the logic.
In conjunction with the Gold Maestro, the ultimate distributed network motion controller, and the other members of the Gold Line of intelligent servo drives, state-of-the-art solutions for the most challenging multi-axis motion applications can be easily implemented, with a short development cycle while maintaining high performance.
Gold Whistle Highlights:
- Gold Line core motion control technology
- Ultra-compact, highest power density
- Highly efficient, high bandwidth performance
- Multiple communication options: EtherCAT, CANopen, USB, Ethernet
- Supports a wide variety of feedback sensors
- Advanced filtering and gain scheduling options for enhanced dynamic performance
- Vector control sinusoidal commutation
Feature | Units | 1/100 | 2.5/100 | 5/100 | 10/100 | 15/100 | 20/100 |
---|---|---|---|---|---|---|---|
Minimum supply voltage | VDC | 12 | |||||
Nominal supply voltage | VDC | 85 | |||||
Maximum supply voltage | VDC | 95 | |||||
Maximum continuous power output | W | 80 | 200 | 400 | 800 | 1200 | 1600 |
Efficiency at rated power (at nominal conditions) | % | > 99 | |||||
Maximum output voltage |
| > 95% of DC bus voltage at f = 22 kHz | |||||
Auxiliary power supply | VDC | 12 to 95 VDC | |||||
Amplitude sinusoidal/DC continuous current | A | 1.0 | 2.5 | 5 | 10 | 15 | 20 |
Sinusoidal continuous RMS current limit (Ic) | A | 0.7 | 1.8 | 3.5 | 7 | 10.6 | 14.1 |
Peak current limit | A | 2 x Ic |
Feature | Units | 3/200 | 6/200 | 9/200 |
---|---|---|---|---|
Minimum supply voltage | VDC | 12 | ||
Nominal supply voltage | VDC | 170 | ||
Maximum supply voltage | VDC | 195 | ||
Maximum continuous power output | W | 480 | 960 | 1450 |
Efficiency at rated power (at nominal conditions) | % | > 99 | ||
Maximum output voltage |
| > 95% of DC bus voltage at f = 22 kHz | ||
Auxiliary power supply | VDC | 12 to 95 VDC | ||
Amplitude sinusoidal/DC continuous current | A | 3 | 6 | 9 |
Sinusoidal continuous RMS current limit (Ic) | A | 2.1 | 4.2 | 6.3 |
Peak current limit | A | 2 x Ic |
Feature | Units | All Types |
---|---|---|
Weight | g (oz) | 55 g (1.94 oz) |
Dimension | mm (in) | 55 x 46 x 15 mm (2.2" x 1.8" x 0.6") |
Mounting method | PCB mount |
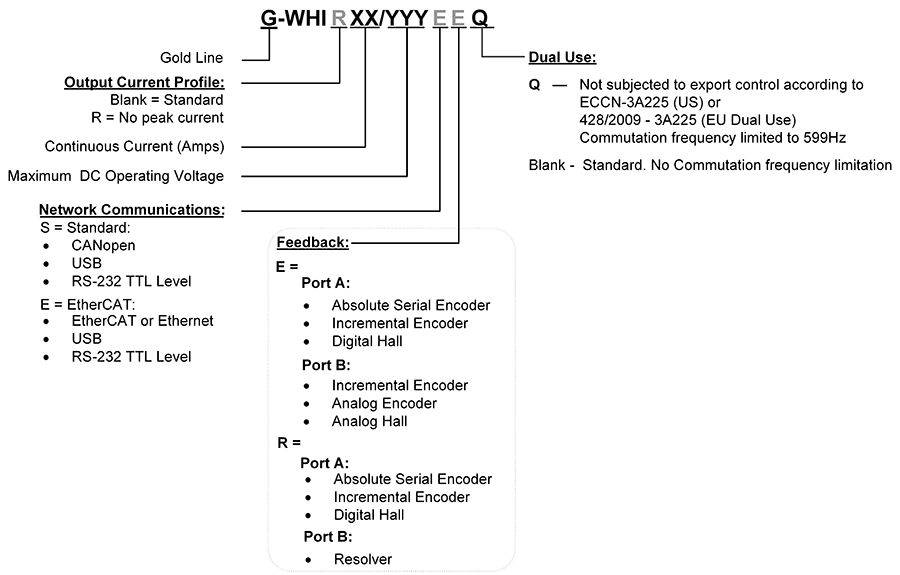