Background
Laser cutting offers clear advantages over traditional manufacturing methods. Its combination of highly focused energy and pressure allows for cutting on a much smaller and narrower area of material, which significantly reduces heat waste and scrap levels. When an innovative laser equipment manufacturer sought to produce next-generation laser-cutting machine, Elmo’s servo drives and controller proved the best fit.
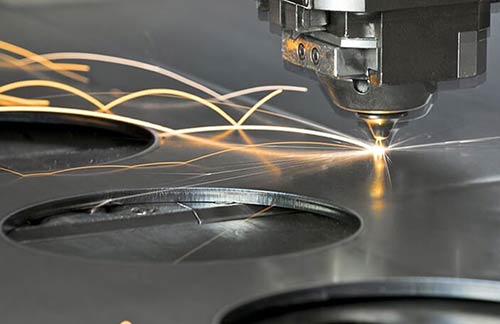
Read this case study to learn about:
- Powerful high-density Gold servo drives controlling the Gantry, X and Theta motors as well as the laser’s power according to the path’s speed.
- Controlled PWM Outputs along the laser’s cutting path.
- The Gold Maestro (GMAS) distributed network controller supporting smooth trajectory planning, ensuring highly accurate and smooth continuity in velocity and accelerations/decelerations over arc motions.
The Machine’s Requirements
A new high-end laser cutting machine had to be developed for the manufacturer’s new project for the Intel Company. A new laser cutting machine included Gantry (Y1, Y2), X and Theta axes as the main axes. Empowering these axes and orchestrating the motion control posed a big challenge, as very strict technical requirements for motion trajectory, OC performance and repeatability of the arc accuracy had to be met.
The Elmo Motion Control Solution
- Gold servo drives
- Gold Maestro Controller
Four Gold servo drives were tightly integrated onto a custom PCB of the four axes, and fitted inside the cutting machine. In addition, Elmo’s Multi Axis Controller with IO extensions was introduced to manage the Elmo’s fieldbus. Together with its real time core and Elmo Application Studio Graphical User Interface, it represents the axes as if they were directly connected, providing complete and easy control with recording and analysis tools.
During the simulation of the laser machine, Elmo was able to demonstrate and test its 2D laser cutting ability with automatic theta axis change as a function of the 2D tangential (normal) axis orientation. The drives also had the ability to output a 2D OC pulses for laser intensity control (On/Off laser type). The intensity of a PWM laser type as a function of the X,Y vector velocity was also fully controlled. In addition, the machine has demonstrated the ability to operate the whole system (X, Y, and Theta) and automatically control the laser intensity from G-Code (.Cad files) tool, including path design, configuration, M-file creation, simulation and execution. A new continuous motion path was introduced to the customer for the 2D OC function which is used for triggering the laser.
Gold Maestro
Advanced Ethercat, Multi- Axis Motion Controller
The Outcome
Integrating Elmo’s best-in-class pin based high performance servo drives and smart controller in the laser cutting machine provided a complete solution for the customer, including G code laser control and some special functions. The single axes and vector position follow errors were very low and met the customer’s requirements, as well as point interval accuracy and roundness tolerance.