Manufacturing and testing wafers is an integral part of the semiconductors fabrication process. Today’s requirements for a Wafer Inspection Machine include high performance, high accuracy servo drives that could ensure 24/7 production with minimum maintenance time and highest possible reliability. When an innovative test equipment manufacturer sought to produce next-generation Inspection Machine, Elmo’s servo drives and controller proved the best fit.
Read this case study to learn how:
- Error correction feature helps the system reach the final target of 10nm accuracy.
- Notch finder function enables to locate the wafer at the highest rotating speed.
- Proprietary Auto-focus feature improves the machine’s throughput, allowing the wafer to reach its measurement target already focused.
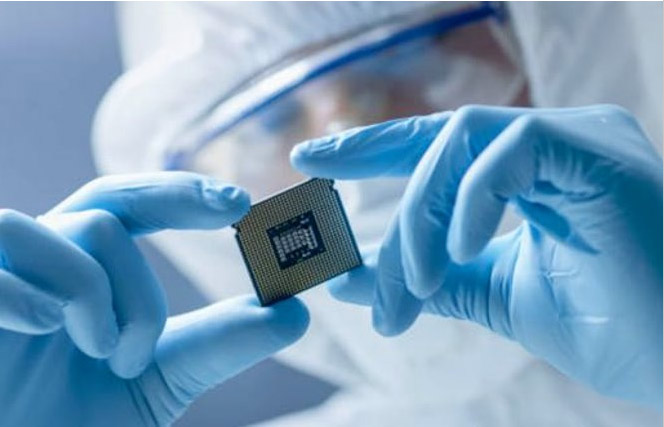
Machine requirements
For a leading semiconductor inspection machine builder, servo performance plays the most demanding and important part in the system. With system resolution of 1nm and challenging dynamic requirements, the manufacturer needed to produce an innovative high-performance inspection stage with unique characteristics. The existing machine included 4 inspection axes, while 6 more axes, powered by Elmo’s drives, had to be integrated in the stage. As this stage is a very sensitive component deep inside the machine and near the wafer, it was crucial to “engineer” every small detail and confirm the machine’s reliability for many years of operation.
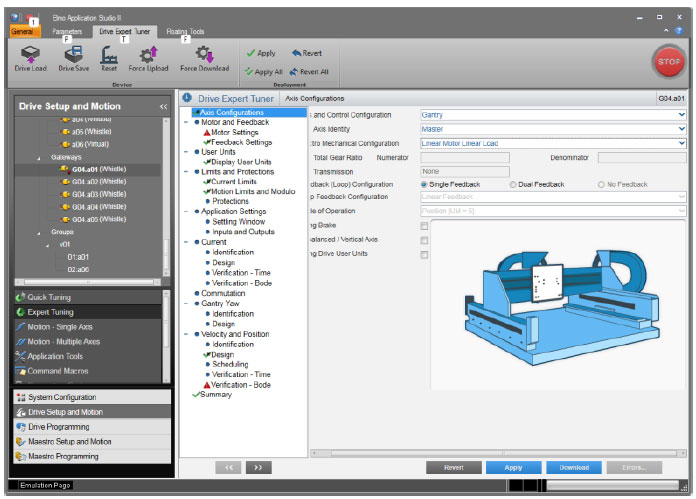
Motion control solution
- Gold Whistle servo drives
- Gold Maestro Controller
Gold Maestro
Advanced Ethercat, Multi- Axis Motion Controller
Gold Whistle
Miniature Servo Drive
20A/100VDC, 9A/200VDC
Six Gold Whistle drives were tightly integrated onto a custom PCB and fitted inside the stage’s moving parts, right near the corresponding motor and encoder, shortening the phases and encoder cable to minimum. All drives are chained with an EtherCAT network to Elmo’s Gold Maestro master controller which manages the system in 500µSec cycle time. The system can be easily scaled up with more axes simply by adding more axes to the EtherCAT network and assigning their address. Elmo’s Gold Maestro is running up to 16 paralleled programs that can perform asynchronous sequences – the machine’s Host computer just triggers the required sequence such as “load wafer” and the Gold Maestro will manage the sequence and report back with an event. Using this asynchronous mechanism saves computational resources from the host computer, as the host does not have to waste time on polling for the sequence status.
As the drives are exposed to constant vibrations and shocks, it was crucial to use a bullet proof well proven electronics that can withstand such conditions. The heat generated by the drives proved negligible, compared to the heat generated by the motors themselves, as for every 100 watts of mechanical power the motor will generate approximately 10W of heat, where the drive will generate only 1W thanks to its 99% of proven efficiency.
The stage mechanics needed to reach a final target of 10nm accuracy, which was no easy task considering that none of the stage’s X,Y,Z and Theta axes is 100% strait, flat, accurate or rigid. Elmo introduced a 3D Error Correction feature, which relies on a preloaded Error Correction tables that represent the stage’s inaccuracy, and automatically compensates the positioning by taking into account the inaccuracy data. The Elmo Application Studio environment incorporates advanced automated tools for measuring these mechanical errors, providing a simple to use GUI.
Each one of Elmo’s Gold Drives in the system is managing the cascaded Position-Velocity-Current closed loops in a cycle rates of up to 20KHz. The powerful DSP also manages more than 10 inline high order filters of any kind: Low Pass / Notch / Anti- Notch / bi quad/ lead-lag, some of them are changing dynamically according to the motion. Non-linear special algorithms are also implemented to improve settling times.
The drives incorporate a Notch finder function, which is a sequence where the machine is searching for the orientation of the newly arrived wafer. The task is to rotate the Theta axis until the notch – a special V mark on the wafer’s edge – is detected by the dedicated sensor, and report its angle back to the host. Faster notch finding means higher wafers per hour, and for this reason, this simple task is being performed in the very low level of the drive, where the analog signal of the wafer’s edge is sampled at 20KHz sampling rate and is able to detect the notch mark at the highest rotating speed.
The wafer’s inspection also incorporates an embedded camera. Every measurement point is captured by a high resolution, high magnitude optical camera with a fixed lens. Focusing the camera is done by slightly moving the wafer up / down (the Z axis of the stage) according to a focus sensing hardware. In order to improve the throughput, the focusing motion is being done while the XY stage is moving between the measurements points, allowing the wafer to reach its measurements target already focused. As this function incorporates special HW interface and special algorithms, Elmo invested in this custom feature specifically for this application. Such customized features are relatively easy to implement due to a flexible FPGA inside Elmo’s Gold Drive.
The Outcome
Integrating Elmo’s best-in-class pin based high performance servo drives deep inside the innovative inspection stage allowed to dramatically improve the wafer inspection machine’s performance. The drives’ customized features such as enabling auto-focus of the optical camera lens, incorporating a notch finder to help locate the wafer, and automatic error correction have significantly enhanced the machine’s accuracy, efficiency and speed.